Mar 09, 2020 PID Control System Design and Automatic Tuning using MATLAB/Simulink is intended for undergraduate electrical, chemical, mechanical, and aerospace engineering students, and will greatly benefit postgraduate students, researchers, and industrial personnel who work with control systems and their applications. Sep 06, 2011 With minimum information, the PLC controller is connected to the control loop and during the auto tune process the plant reaction to the proprietary stimulus algorithm, is measured and compared in controlled iterations. The PID Server utility enables the control engineer to auto-tune PID loops for both the Vision and M90/91 controller series.
This example shows how to automatically tune a PID Controller block using PID Tuner.
Introduction of the PID Tuner
PID Tuner provides a fast and widely applicable single-loop PID tuning method for the Simulink® PID Controller blocks. With this method, you can tune PID controller parameters to achieve a robust design with the desired response time.
A typical design workflow with the PID Tuner involves the following tasks:
(1) Launch the PID Tuner. When launching, the software automatically computes a linear plant model from the Simulink model and designs an initial controller.
(2) Tune the controller in the PID Tuner by manually adjusting design criteria in two design modes. The tuner computes PID parameters that robustly stabilize the system.
(3) Export the parameters of the designed controller back to the PID Controller block and verify controller performance in Simulink.
Open the Model
Open the engine speed control model with PID Controller block and take a few moments to explore it.
Design Overview
In this example, you design a PI controller in an engine speed control loop. The goal of the design is to track the reference signal from a Simulink step block scdspeedctrlpidblock/Speed Reference
. The design requirement are:
Pid Controller Autotuning
Settling time under 5 seconds
Zero steady-state error to the step reference input.
In this example, you stabilize the feedback loop and achieve good reference tracking performance by designing the PI controller scdspeedctrl/PID Controller
in the PID Tuner.
Open PID Tuner
To launch the PID Tuner, double-click the PID Controller block to open its block dialog. In the Main tab, click Tune.
Initial PID Design
When the PID Tuner launches, the software computes a linearized plant model seen by the controller. The software automatically identifies the plant input and output, and uses the current operating point for the linearization. The plant can have any order and can have time delays.
The PID Tuner computes an initial PI controller to achieve a reasonable tradeoff between performance and robustness. By default, step reference tracking performance displays in the plot.
The following figure shows the PID Tuner dialog with the initial design:
Display PID Parameters
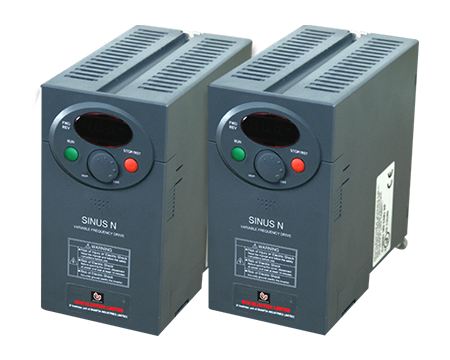
Click Show parameters to view controller parameters P and I, and a set of performance and robustness measurements. In this example, the initial PI controller design gives a settling time of 2 seconds, which meets the requirement.
Pid Control Auto Tuning Parts
Adjust PID Design in PID Tuner
Pid Control Auto Tuning Parts
The overshoot of the reference tracking response is about 7.5 percent. Since we still have some room before reaching the settling time limit, you could reduce the overshoot by increasing the response time. Move the response time slider to the left to increase the closed loop response time. Notice that when you adjust response time, the response plot and the controller parameters and performance measurements update.
The following figure shows an adjusted PID design with an overshoot of zero and a settling time of 4 seconds. The designed controller effectively becomes an integral-only controller.
Complete PID Design with Performance Trade-Off
In order to achieve zero overshoot while reducing the settling time below 2 seconds, you need to take advantage of both sliders. You need to make control response faster to reduce the settling time and increase the robustness to reduce the overshoot. For example, you can reduce the response time from 3.4 to 1.5 seconds and increase robustness from 0.6 to 0.72.
The following figure shows the closed-loop response with these settings:
Write Tuned Parameters to PID Controller Block
After you are happy with the controller performance on the linear plant model, you can test the design on the nonlinear model. To do this, click Update Block in the PID Tuner. This action writes the parameters back to the PID Controller block in the Simulink model.
Auto Tuning Pid Control
The following figure shows the updated PID Controller block dialog:
Completed Design
The following figure shows the response of the closed-loop system:
The response shows that the new controller meets all the design requirements.
You can also use the Control System Designer to design the PID Controller block, when the PID Controller block belongs to a multi-loop design task. See the example Single Loop Feedback/Prefilter Compensator Design.